电磁离合器胀套和联轴器
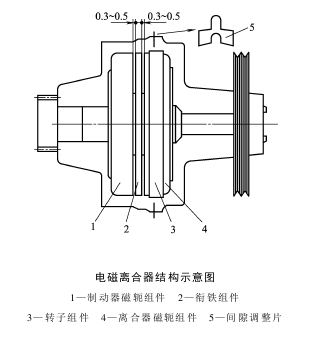
电磁离合器用于剑杆织机、喷气织机和喷水织机的传动系统,可实现主动部件和被动部件快速可靠的结合、分别、传递动力、制动、定位。
离合器(下图)是由制动器磁轭组件1,离合器磁轭组件4,衔铁组件2,转子组件3,4个主要组件组成。
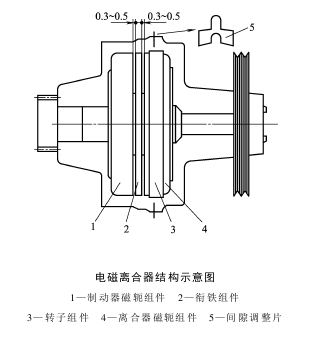
离合器工作原理是当离合器磁轭通电制动器磁轭断电,离合器磁轭产生电磁力通过转子吸合衔铁,使转子摩擦片和衔铁产生肯定摩擦力,实现主动件和被动件的可靠结合,传递动力,使织机运转。当制动器通电,离合器断电,制动器磁轭产生电磁力,离合器磁轭电磁势消逝,衔铁借助弹簧片的弹力和离合器磁轭、转子脱开,制动器磁轭吸合衔铁,使衔铁和制动器磁轭摩擦片产生摩擦力。
离合器是磁轭通电产生电磁力吸合衔铁、衔铁和摩擦片产生摩擦力来传递动力,所以衔铁和转子摩擦片间隙务必要调整在0.3~0.5mm之间,可用间隙调整片5(图18-1)调整到佳位置。
一、单片电磁离合器
无梭织机中的电磁离合器属于单片电磁离合器产品范围内的一种专用离合器,其产品主要分为组合离合器、电磁制动器、电磁离合器和牙嵌离合等类型。这类产品规格、参数、性能、安装尺寸、制动扭矩(动扭矩)、传动扭矩(静扭矩)和其他性能指标等特点,均以满足新型织机的需要为前提。
由德国、日本、美国等出名离合器专业厂家生产,并成功地将多片电磁离合器有效结构理论推广到织机专用单片电磁离合器中,改善了单片电磁离合器传统结构,完善了织机专用离合器结构性能,促使该产品性能极大地提高。如衔铁结构由单磁路单衔铁进展到双磁路单衔铁、双磁路双衔铁,实现了衔铁重量减轻。又能在不改变离合器或制动器原结构尺寸的基础上,使该类产品扭矩成倍增加,适应无梭织机转速增加的需求,促进了织机进展和效率的提高。和通用型离合器相比,该类产品不成系列,更新换代快,随织机的更新而淘汰。而现代新型无梭织机高速、高效、高可靠性实现又和织机专用离合器的进展息息相关,已成为单片电磁离合器一个新的进展门类。
织机专用离合器有些是通用型离合器变型产品,有的则是为织机特意设计的。不管哪类产品,均要适应织机对安装、调试、维修、高传递扭矩和高制动扭矩的要求,实现无梭织机快速起动、快速制动等方面的特性。
单片电磁离合器和制动器、组合离合器及失电动器等均是无滑环,干式单片,具有结构紧凑、响应快速、寿命长久、使用可靠等特点,目前已广泛地应用于布料机械产品和装置中。在这些机械和装置中所使用电磁离合器和制动器主要作为自动化执行元件。
为确保离合器和制动器的使用寿命,电磁离合器和制动器、组合离合器、失电制动器等产品的摩擦片,需采纳高性能、耐高温的非石棉基摩擦材料。
二、电磁离合器的分类
(1)电磁离合器分为DLD5—40型、DLD6—160A型、DLD6—160/F型、DLD6—160/E型、DLDF—350型和DLDF—550型。
(2)电磁制动器分为DZD5—80/A型、DZD5—160型、DZD5—160/A型、DZD5—160/C型、DZD5—160/D型、DZD5—160/F型、DZD5—160A型、DZDF—350型、DZDF—550型、DZDF—320/C型、DZDF—320/D型、DZDF—320/E型、DZD5—320/X型和DZD5—250/B型。
(3)组合离合器分为DLZF—350Ⅰ型、DLZF—350Ⅱ;450Ⅰ;500Ⅰ型、DLZF—400型、DLZF—450Ⅱ型、DLZF—500Ⅱ型、DLZF—500Ⅲ型、DLZF—600型、DLZF—900型、DLZF—900A型、DLZF—1000型、DLZF—500ⅡA型、DLZF—850型、DLZF—350I型、DLZF—350IV型、DLZF—1100型和DLZF—1100A型。
(4)牙嵌离合器分为DLFY—200型、DLFY—900型、DLFY—566慢速型、DLFY—566寻纬型和DLZF—500型等。
三、牙嵌电磁离合器
牙嵌电磁离合器,是在牙嵌机械离合器基础上进展起来的,其中齿型部分和牙嵌机械离合器基本相同,有梯形、三角形、对称齿、非对称齿等多样形式。按牙型划分可分为细牙和粗牙两类。按动作划分可分为定位齿(不等距齿)和非定位齿(对称和不对称等距齿),得电和失电等
类型。像一般电磁离合器一样,早期牙嵌电磁离合器均采纳滑环电刷供电,近代新型牙嵌电磁离合器均采纳单片电磁离合器基本结构形式,即衔铁和转子被端面齿盘所替代,磁轭是固定不转动的方便供电,提高了产品的可靠性。
牙嵌失电定位离合器和牙嵌失电离合器动作一样,即通电脱开,断电(失电)结合,但区别在于结合时端面齿为不等距齿,保证了每次结合时,相对位置不变。牙嵌失电离合器主要用于结合状态大于脱开状态,或工作不同意过热和有电火花的环境。此外,牙嵌失电定位离合器还应用在对定位有要求的场合。
牙嵌电磁离合器和其他电磁离合器相比,扭矩体积比较大。转速不丢转无滑差,对传动比要求非常严格和分支休闲的情况更合适。一般均用在体积空间小,低速大扭矩场合。不宜在高速传动系统中使用,选用时扭矩安全系数大,至少是额定扭矩的2.5~3.0倍,牙嵌离合器对振动和偏心安装很敏感,额定扭矩随着转速升高而下降,其下降率因端面齿型和结构而区别。当牙嵌离合器转速超过电动机的额定转速(1500r/min以上)时,此时安全系数应是电动机额定扭矩的6~7倍。若选择扭矩容量偏小,在传递大扭矩时电动机失控前,离合器就会自动脱开,此时牙嵌离合器传动特性就不能保持。
四、胀紧联结套
胀紧联结套是国际上广泛用于各种载荷下机械联结的先进机械基础件,用于安装于电磁离合器和主轴的连接。欧美国家首先在重载荷机械中使用了这项新技术。现已推广到其他各种机械行业,胀紧联结套在国际上起始于20世纪70年代初期,我国于20世纪80年代初就对该产品进行了研制,并首先在各种重型机械中推广应用,于1986年国家制定了通用型胀套GB5867—86标准。经过近二十年实践已完成了对该标准中全部规格品种的开发,并推广到通用机械等各种机械中,促进了机械行业产品技术进步。
胀套联结是一种新型联结方式,它靠拧紧高强度螺栓使胀套和轴间或套间包容面间产生正压力,相伴产生摩擦力,实现负荷传递的一种无键联结装置。它和一般过盈的无键联结、有键联结的传统机械联结方式相比有许多独特的优点和特性。
(1)制造和安装简单:安装胀套的轴和孔后整理不像过盈配合那样要求高精度的制造公差,安装胀套也无需加热、冷却或使用加压设备,只需将螺钉按规定扭矩值拧紧即可。
(2)有良好地互换性,且拆卸方便:拆卸时,只需松开压紧螺栓,并用顶出螺栓拧动加压后,即可解除联结状态,将胀套和联结零件分别。
(3)胀套联结可以承受重负荷:其结构可做成多种式样,为适应安装负荷需要,一个胀套不够,还可多个串联组合使用。
(4)胀套联结是一种周密无间隙、无键的联结,具有传动精度和传动效率高、使用寿命长、不易腐蚀等优点。在工作中无相对滑动,不会磨损。特别适宜在各种高精度传动和伺服机构中使用。
(5)胀紧联结套在轴向安装时,不需要轴向任何固定就可以方便地调整其轴向所需位置尺寸及零件的相对位置。
(6)随着应用范围的扩大,机械中各种复杂联结形式都可以用特别胀紧联结套替代。简化传动结构或成为机械零部件中一个组成部分,如无间隙的膜片联轴器。
(7)胀套选用可使主机配套商品化率高,便于主机技术进步和进展和产品更新。
(8)胀紧联结套可在-30℃~200℃温度范围之间工作,并可以根据工作环境和介质的不同,选择多种不同材料制作。
五、联轴器
联轴器是机械传动系统中连接两轴或轴和回转部件,在传动休闲和动力过程中同步回转而不脱开的一种装置。联轴器伴随机械产品而生,为了适应各种机械传动和安装方式的需求,联轴器品种类别繁多。但主要分刚性联轴器和挠性联轴器两大类。刚性联轴器由于不能调整两轴间径向及角度偏差,转动惯量大等原因,现已很少使用,在近代机械中已被淘汰。挠性联轴器兼有作为轴系中的弹性元件而起调节频率、减振、补偿两轴相对位移、缓冲和安全作用。一般分为无弹性元件联轴器、非金属弹性元件联轴器和金属弹性元件联轴器。后两者除具备前者补偿两轴相对位移的功能外,还具有缓冲和减振作用,但在传递扭矩的能力上,因受弹性元件强度的限制,一般不及前者。平行轴联轴器,可用于同一轴线上的两轴向的连接。除此之外其他刚性联轴器已很少有联轴器专业厂家生产。
新型联轴器,是泛指挠性联轴器中的先进产品。随着机电产品朝着高速、高效、高精度的方向进展,传统结构的联轴器已不能适应进展的需要。伴随着新材料、新技术和新工艺的进一步研究,部分传统产品结构和材料已被淘汰更新,新型联轴器也应运而生,正逐步得到用户青睐。如梅花弹性体均采纳大阻尼材料以提高固有频率和阻尼系数,使减振性能极高。其梅花形弹性体的弹性变形不是靠泊松效应,而是借助于弧状曲面在工作中极易变形来实现的,比传统结构更先进。还有鼓形齿联轴器、中间内齿套采纳高弹性、高强度、耐油、耐腐蚀、耐冲击的有机材料。
为适应现代机械传动中高速、低惯量、无间隙的要求,膜片式联轴器和轴连接均采纳成对胀环来实现无键连接。采纳该结构的膜片联轴器更适合用于伺服传动系统传动机械中,操作传动间隙,减少伺服系统死区,提高机械传动的定位精度和伺服性能。
胀紧联结套是一种新型联结件,可实现无键联结。新型联轴器产品结构已经比较完善,和其他传动件如安全离合器等组合形成新的传动件产品。
联轴器的种类很多,品种规格更多。目前使用较多的为膜片联轴器、梅花型联轴器、鼓形齿式联轴器、十字轴万向联轴器和胀套型联轴器等。
AAAVSGREHTRY45FGHTYHCGER AAA
版权声明
本文仅代表作者观点,不代表本站立场。
发布的有些文章部分内容来源于互联网。如有侵权,请联系我们,我们会尽快删除。
发表评论